
Full-scale removal of the concrete began at 4:30 am on October 1. On September 30, workers began using high-pressure water-at pressures up to 25,000 pounds per square inch-to cut and remove the concrete from an 8-feet wide by 6-feet tall test section of the concrete containment wall. An early step involved loosening and removing the horizontal tendons from the containment wall in the region where the opening would be cut. Seven minutes later, the contractor hired to cut through the containment wall was authorized to begin that work. They continued cooling the reactor water down over the next few hours and entered Refueling mode at 4:51 pm that afternoon. They shut down the reactor at 12:29 am September 26. The operators began reducing the reactor power level at 7:03 pm on September 25, 2009, to enter the refueling outage. The concrete has not yet been poured in that section of containment, so the metal reinforcing bars and horizontal tendon sleeves (the vertical rows of white dots on either side of the equipment hatch) embedded in the concrete are visible. Figure 2 shows the equipment hatch in late November 1972 during plant construction. The containment featured a large round opening called the equipment hatch. This containment design was used for more than half of the PWRs operating in the United States. These tendons functioned like reinforcing bands-workers tightened, or tensioned, them to give the concrete wall additional strength against the internal pressure that could occur during an accident. Embedded in the concrete walls were 5.25-inch round tendons encased within metal sleeves.

Behind it were 42-inch thick concrete walls and a 36-inch thick concrete dome. The 0.475-inch thick steel liner formed the inner surface of the containment wall. The containment at Crystal River 3 was a 3-D post-tensioned concrete cylinder with a steel liner. The vertical portion of containment is a cylinder about 137 feet in diameter.
POWER FACTORY 15 CRACK GENERATOR
In front of the steam generator on the right is the pressurizer. The reactor vessel is flanked by the two larger steam generators. The reactor core is the green rectangle within the capsule-shaped reactor vessel. Since the first steam generator replacements more than two decades earlier, so many PWRs had performed this exercise that it was almost routine.įigure 1 shows a simplified side view of the containment structure at Crystal River 3. The original steam generators were wearing out and were to be replaced with steam generators made from materials more resistant to wear and tear. Workers planned to replace the steam generators during the outage. Operators shut down the reactor on September 26, 2009, to begin the plant’s 16th refueling outage. Refueling Outage and Steam Generator Replacements
POWER FACTORY 15 CRACK LICENSE
The NRC issued the reactor operating license on December 3, 1976. When the cost of fixing the broken containment rose too high, the owner opted to permanently shut down the facility before its original operating license expired.Ĭrystal River 3 is located on the western coast of Florida and featured a pressurized water reactor (PWR) designed by Babcock & Wilcox. The replacement steam generators would enable the reactor to operate through the end of its current operating license period as well as to the end of a renewed license.īut those plans changed drastically when the process of cutting an opening in the concrete containment wall for the steam generator replacement inflicted extensive damage to the concrete.

The Nuclear Regulatory Commission (NRC) was reviewing the owner’s application to extend the reactor operating license for another 20 years. During the refueling outage, the original steam generators were scheduled to be replaced. The Crystal River 3 pressurized water reactor in Florida was shut down in September 2009 for refueling.
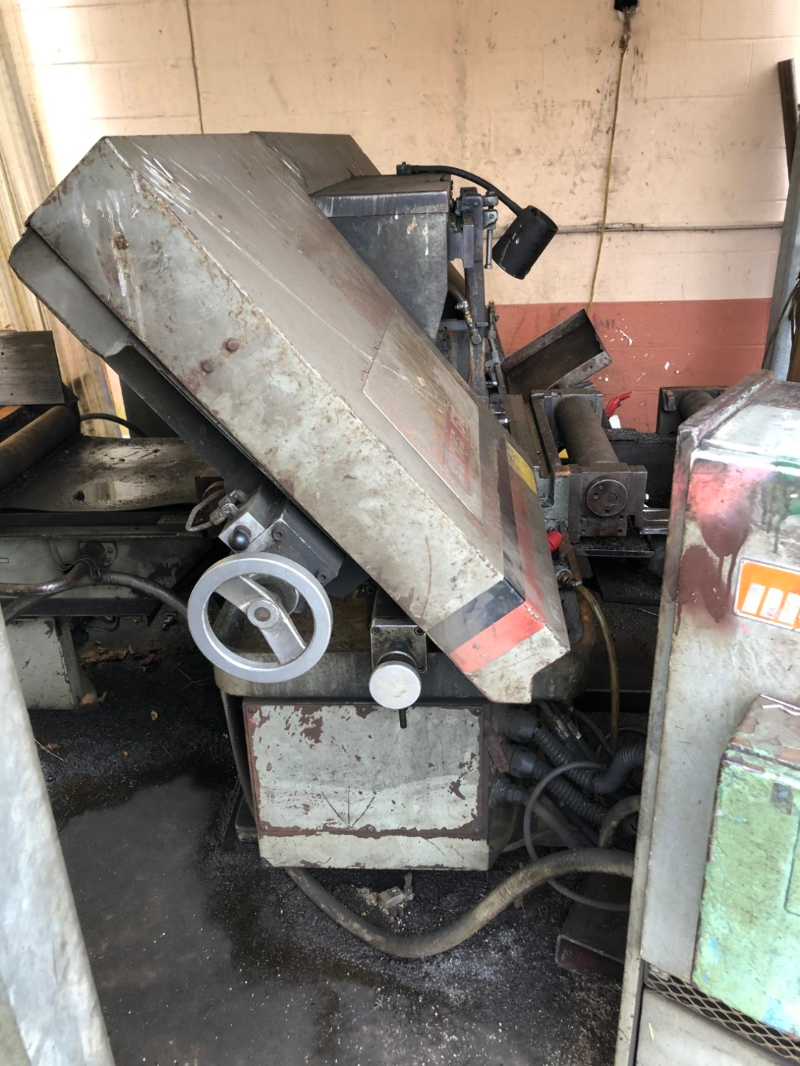

Role of Regulation in Nuclear Plant Safety #10
